PROJECTS
PROJECT TYPE
Functional analysis
Improve overall and operating performance
Process automation
CLIENT
Poultry farm
SECTOR
Food processing
REGION
Centre du Québec
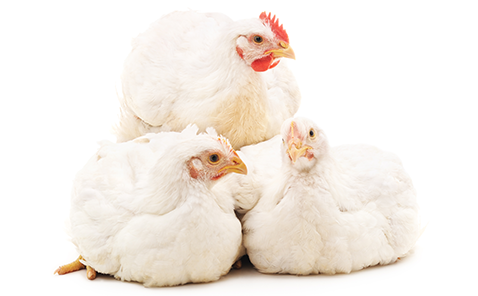
Company
We had the pleasure of working with a large poultry farm housing more than 100,000 laying hens. Our client was a modern business equipped with leading-edge technology in terms of energy efficiency, animal welfare, production systems and process automation.
Mandate
We were tasked with the development of a monitoring and control system to dry droppings. The system had to transform in less than 24 hours 9 tons of wet manure into 3 tons of 90% dry manure. Our client wanted to have a more robust and reliable system, and an easy-to-operate, visually user-friendly operator interface. The following element also had to be included:
- User-friendly diagnosis and alarm page for operators
- Configuration menu accessible only to the director
- Reliable local technical assistance to remotely support and diagnose the system 24/7
- System allowing for quick user control and backup of the interface
Challenges
- Need to effectively replace a not very reliable or user-friendly European system from an equipment manufacturer with poor after-sales service and technical assistance
- Presence of 100,000 laying hens, which means that any drying system disruption quickly leads to serious odour problems that must be avoided at all costs

Benefits
- Local technical assistance
- More robust and reliable system
- Better operator control over the procedure
- Less shutdowns and shortened downtime
- Reduced maintenance costs
- Lower environmental impact and better relations with the community
Solutions
Working together with the client led to implementing the following solutions:
- Replacing electronic boards with a PLC
- Replacing the 6-inch black-and-white interface with keyboard by a 12-inch color touchscreen operator interface that displays more information on a single page and animated motions
- Complete update of all the electrical drawings (power and control) of the drying system
- Implementing a bypass system that allows to temporarily deactivate a sensor to complete a drying cycle
- Training all system administrators and operators

Efficiency gain estimated to + $15,000 annually